CO2 emissions reduction by energy optimization
50% – 100% reduction of energy loss in dynamic interfaces in product population outliers. Higher performance of all products in a production series (population). Elimination of energy loss in a population of products by eliminating friction in dynamic interfaces.
19% energy savings by Robust Design
A simple example for illustrating the effect of over constraints in designs with moving mechanics: a rotation shaft supported by 3 bearings in a frame. The result of a kinematic review of this design is that it is over-constrained in the y-direction by the middle bearing and over-constrained in Rz by all 3 bearings. For this example – the only impact of the “y” over constraint is considered.
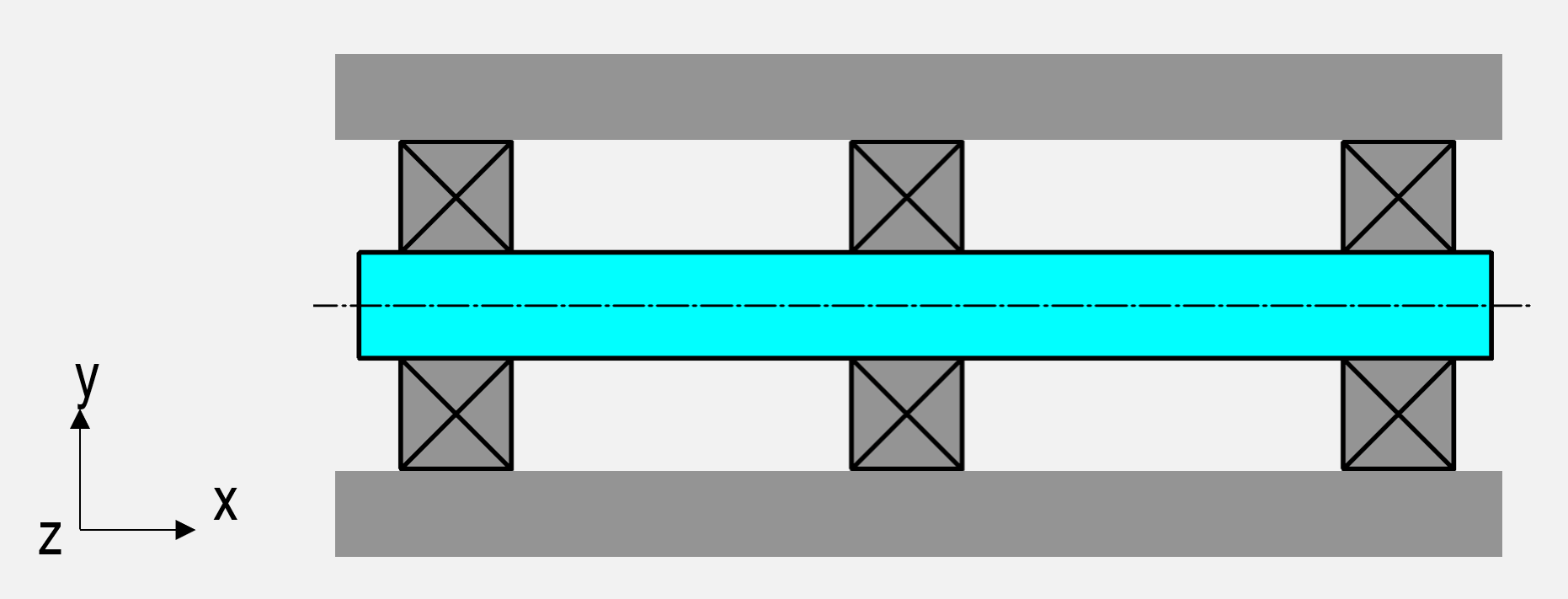
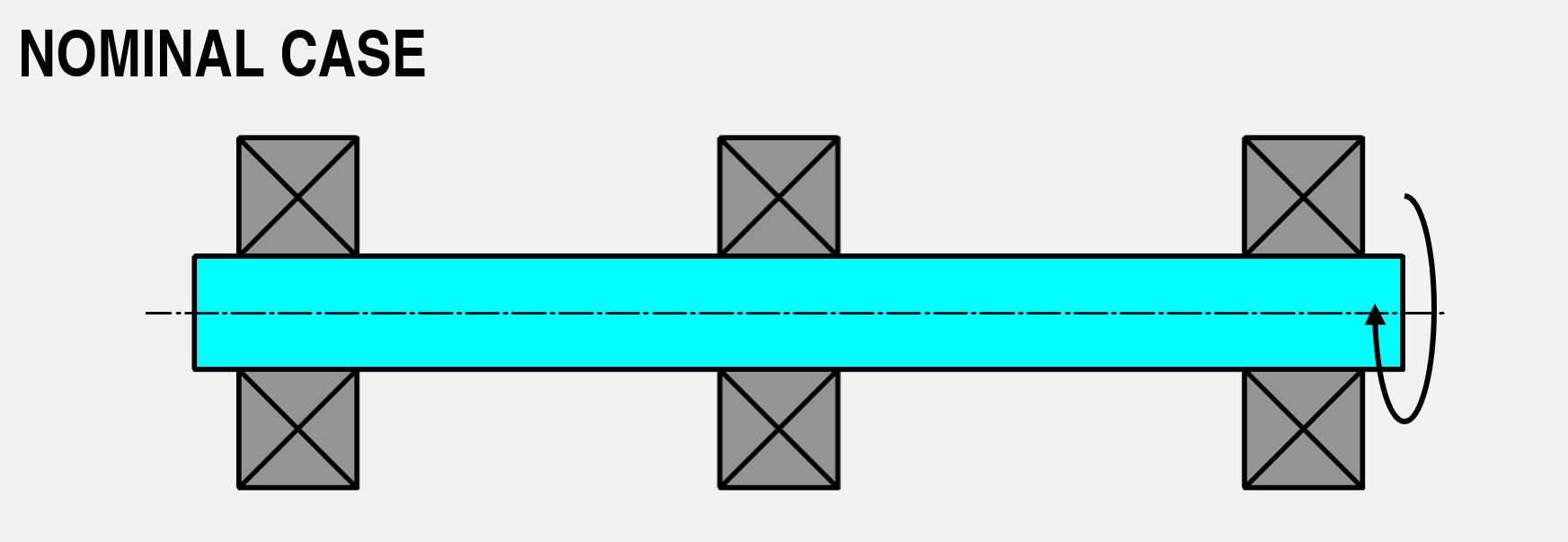
The effect of the over constraint in the y-direction is illustrated to the right. A deflation of δ is simulated. For this example, a δ variation of 0.2 mm is assumed (due to tolerance variation).
Simulation of the shaft in FEM (Finite Element Method) results in stiffness of the shaft of:
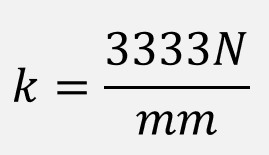
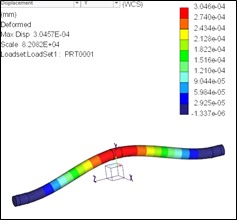
The resulting force, F_R, from the assumed deflection, is given by:

The friction force F_μ can be calculated by multiplying the friction coefficient by the radial force F_R. The friction in the bearing is assumed to be 0.1 – resulting in a friction force F_μ:

The friction force can be used to calculate a torque loss due to the over constraint. This is given by the friction force multiplied by the radius. The radius, in this case, is r = 5mm.

The conclusion is that the over constraint will add an additional 335Nmm in resistance for the shaft to rotate. This torque the user or motor will have to overcome. It will need to be evaluated if it can be accepted.
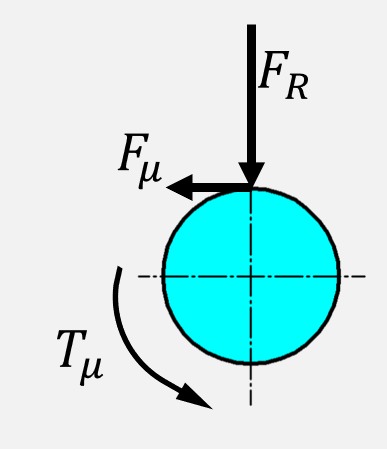
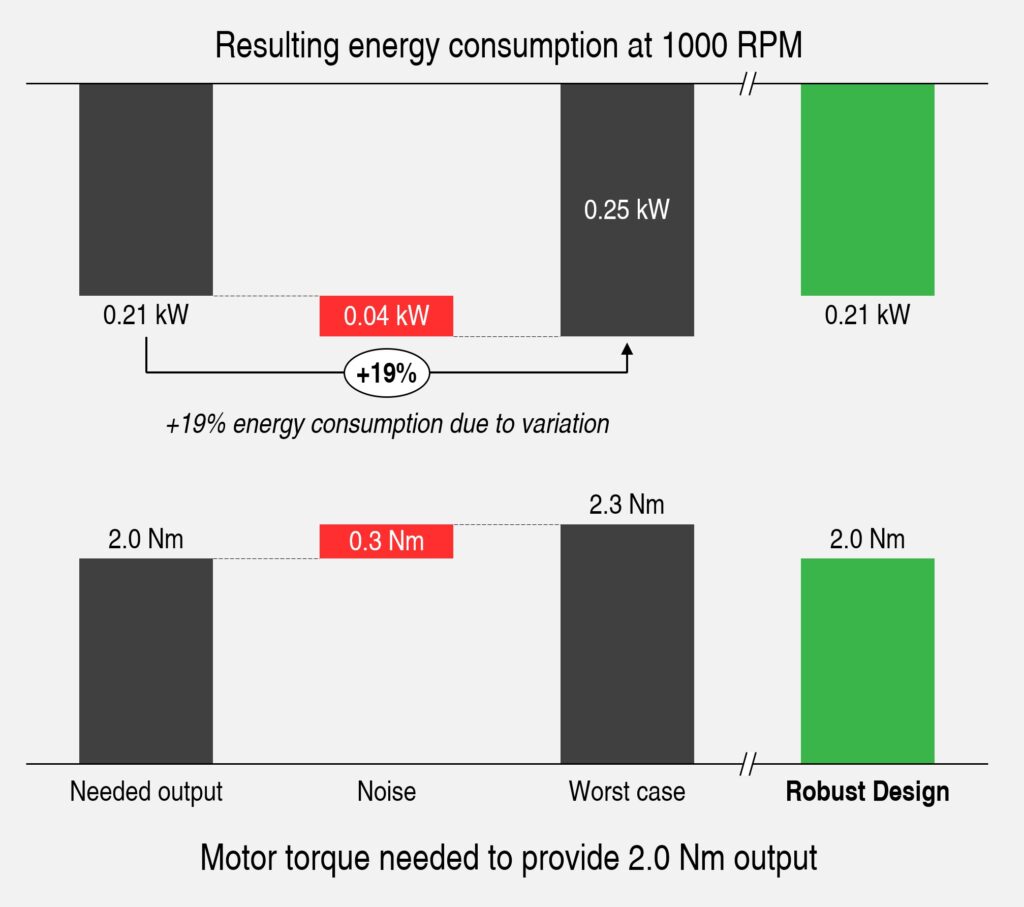
Assuming a fictive case where a 2.0 Nm output is needed from a motor driving the shaft.
Due to the noise from the over constraint in the worst case tolerance scenario, it was calculated that an additional torque of 0.335 Nm is needed.
This is equivalent to 0.04 kW.
In the ideal case where there is no variation – 0.21 kW is needed to provide a 2.0 Nm output (1000 RPM assumed).
In the worst case, the motor will need to provide 2.3 Nm output as 0.3 Nm will be consumed for friction in the system.
When comparing the ideal and worst-case scenarios, it is seen that a 19% additional energy consumption is present.
By Robust Design the noise can be eliminated and thus the additional 19% energy consumption can be saved.
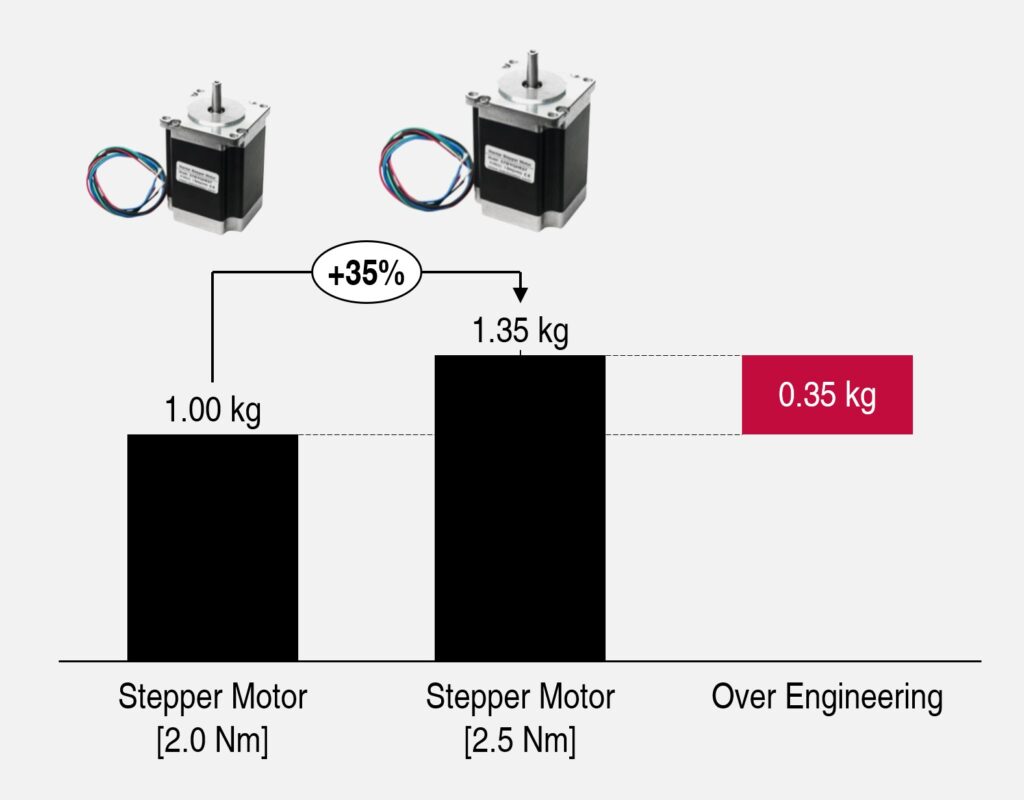
35% reduction of over-engineering
Another effect of the over-constraint design and the need for a larger motor is over-engineering.
To ensure that the product will work during worst case situations (where additional torque is needed – as illustrated above) the designers need to accommodate this situation by dimensioning the product to this worst case. In this example, a motor with a sufficient torque output is needed. In nominal conditions a motor of 2.0 Nm is needed – for the worst case, a 2.3 Nm motor is needed. In many cases a safety factor is needed, hence an even bigger motor is needed. For this example, a 2.5 Nm motor is chosen as this is a standard component.
One of the effects of this is added weight. In this case for a stepper motor the weight difference is 0.35 kg – hence more material consumption in both motor and the rest of the product construction. This is referred to as over-engineering. Furthermore, the cost is often also affected by over-engineering.
Are you interested in hearing more about how Robust Design
can add energy savings to your products?
Book a meeting with us already today